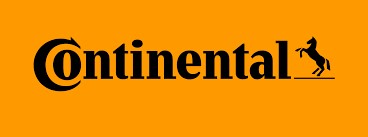
Continental has developed a line for cooling in the hydrogen powertrain of commercial vehicles, which considerably reduces the penetration of ions into the media circuit.
The synthetic rubber line has a mixture of materials the special properties of which make them less susceptible to the leaching of ions from the line material. This reduces the transfer of ions into the cooling circuit of hydrogen drive systems.
The product innovation increases the service life of vehicle components in hydrogen drive systems.
If ions from the line material enter the cooling circuit, this can lead to degradation of the material. In turn, this reduces efficiency and increases the risk of a short circuit or leakage currents in the fuel cell. Washed out ions can, for example, damage the proton exchange membrane (PEM) and shorten its lifespan.
To combat this, Continental is using a mixture of synthetic rubber for cooling in the hydrogen circuit of commercial vehicle drive systems. More specifically, it is a special mixture based on high performance EPDM (ethylene propylene diene rubber) that offers the necessary high resistance against the unwanted leaching of ions.
As part of the move away from oil and gas, many bus and truck fleets as well as commercial vehicle manufacturers are pinning their hopes on hydrogen as a source of energy for drive systems. However, compared to the use of battery generated drive energy, engineers in the vehicle industry currently still face a large number of challenges when it comes to hydrogen. The extremely low density of hydrogen atoms also presents problems for developers.